SMARTER JOB PREP CASE STUDY
IMPROVED PRODUCTIVITY | A MORE EFFICIENT WAY TO PREP JOBS

UNIÓN DIGITAL (IMPRESION A2)
Background
UNIÓN DIGITAL, part of the IMPRESIONA2 GROUP, is a Graphic Services Company, specialising in high quality printing.
With more than 20 years of experience in printing: Catalogues, Books, Magazines and Brochures of all kinds: Artistic, Commercial and Promotional.
UNIÓN DIGITAL‘s facilities are equipped with the latest technology to control all production processes with the highest quality.
When we installed PrintFactory with the INCA Spyder Machine, we placed a trial order for all the systems including 2 Roll to roll solvent and ecosolvent printers with different manufacturers, and 1 flatbed UV printer and new flatbed acquisition from another manufacturer. After Print Factory was installed and colour calibrated, all the machines had the same colours independently of ink type, manufacturer, print configuration, 4 colours vs 6 colours In addition we saved a lot of time not only for prepress and job preparation but also to change one job between machines
Susana Abad of UNIÓN DIGITAL
What Were The Problems?
- Using different RIPs and the time it was taking to prepare jobs in different ways for different printers
- Matching the colour between traditional offset prints and large format digital print
- Rapid growth – expanding through acquisitions and adding new printers meant that they had to standardize operating procedures to achieve consistency
- Getting all machines printing the same colour, not only to print the same campaign on different materials and printers, but also not to ensure that production can continue on any device in the event of a breakdown or problem without wasting time on setting up another printer
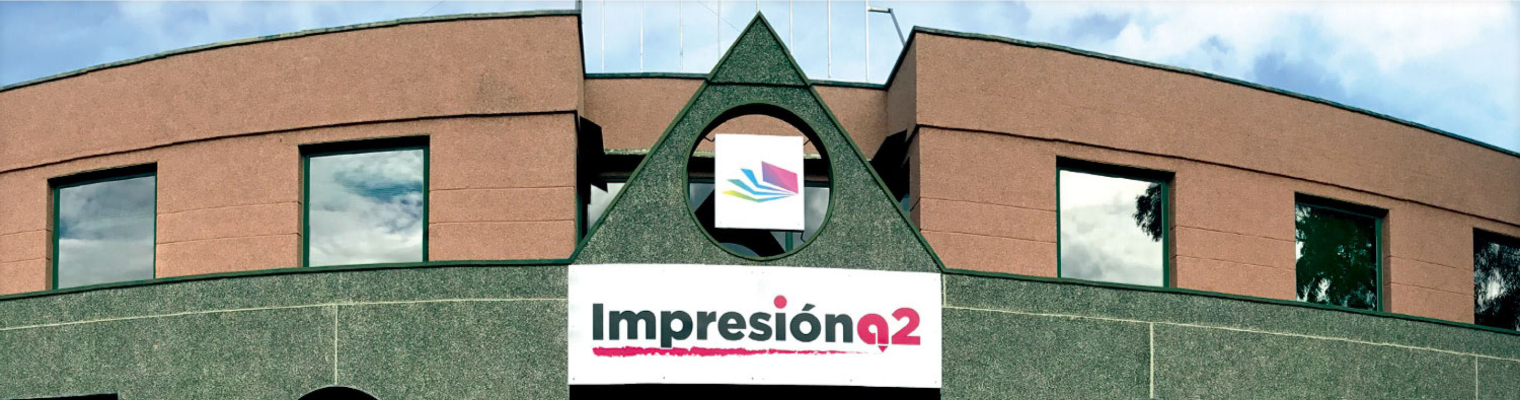
UNIÓN DIGITAL (IMPRESION A2) Story
UNIÓN DIGITAL wanted to improve their productivity but they were losing time and spending money, constantly chasing colour across multiple devices.
UNIÓN DIGITAL was growing with new printer acquisitions and contracts. The new machines came with new inks.
WHAT DID PRINTFACTORY DELIVER?
With PrintFactory software running, colour matching is now guaranteed and easy enough for anyone to do. The costly bottlenecks are no more. This new workflow is boosting UNIÓN DIGITAL’s production by 25%, and their customers confidence in the quality of the finished product has been significantly boosted.
HOW DID WE DO IT?
Behind the scenes, PrintFactory software uses an algorithm that solves all of the problems caused by colour drift.
For the setup, we worked closely with the team to make sure a switch-over didn’t cause disruption. They went for our Production Plan in a Software as a Service (SaaS) format, and we were onsite throughout to get their printers set up and calibrated, first time around. On-site staff training was a given, of course.
PrintFactory’s colour management toolkit and device-link profiling technology is now matching visuals and proofs – time after time after time. Our device-link engine is delivering the colour quality and consistency that UNIÓN DIGITAL needed, across all their devices and substrates, and (as the EcoSave module is using less ink without compromising on colour fidelity) the bottom-line savings are business-wide. The team’s much happier too. Everyone in the business can use the software to get that accuracy.
Because Unión Digital is a company from A2 group, where the main customers are offset printing customers, their main challenge was to match the colour between traditional offset prints and large format digital print. After PrintFactory was installed, the colour and quality was accepted by their customers, with campaigns for the same customers being produced in both formats consistently.
These improvements have boosted the team’s confidence no end.
It’s something that Susana Abad of UNIÓN DIGITAL believes is reflected in the quality of the company’s work: “Our traditional offset customers started to believe in our new digital prints alternatives.”
WHAT IS COLOUR DRIFT?
Colour drift is a change in the colour you’re printing, due to things beyond your control. Things like humidity, equipment wear-and-tear, and stock or substrate changes.
After PrintFactory was installed, we are more confident to accept customer jobs. We know we will match their needs and we can combine all of our systems without losing time in repeat jobs or extra adjustments. We save a lot of time and we have increased our reputation with our customers..
Susana Abad of UNIÓN DIGITAL
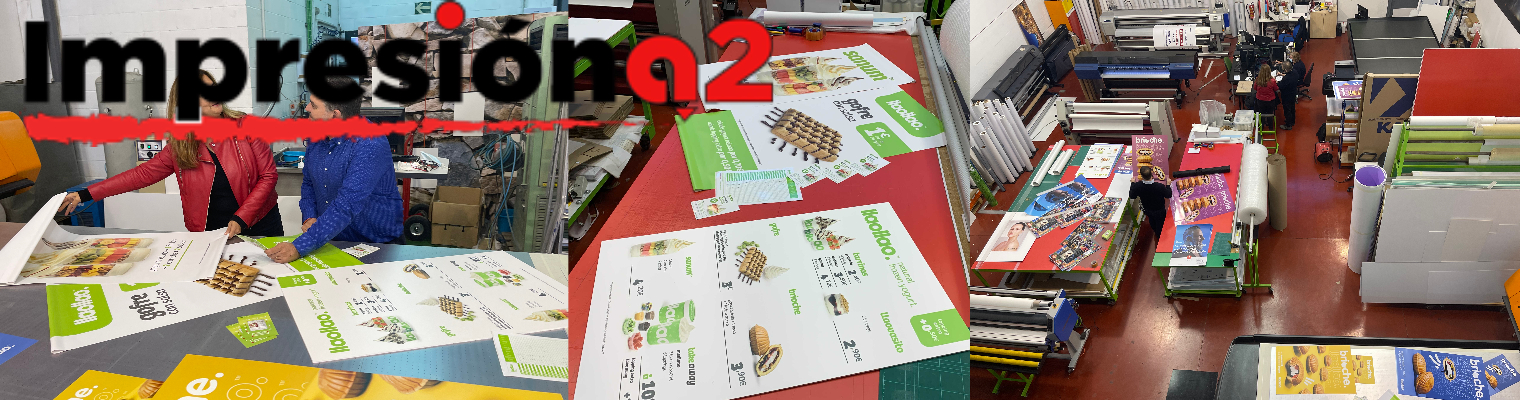